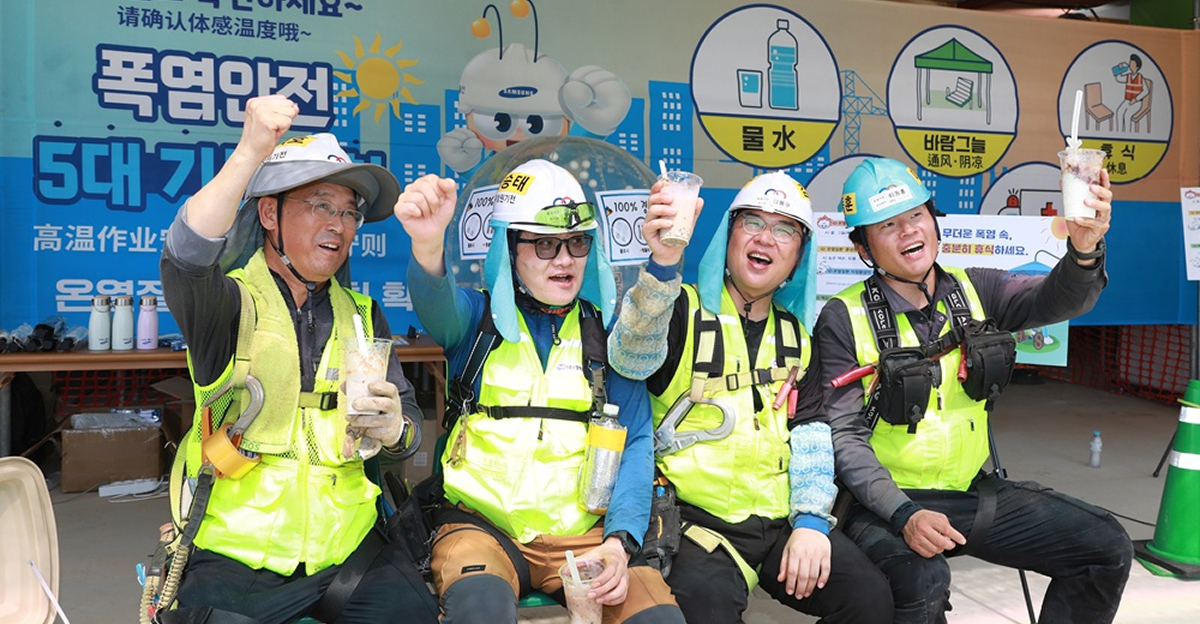
Building in the Heat: How Samsung C&T Is Protecting Construction
August 12, 2025
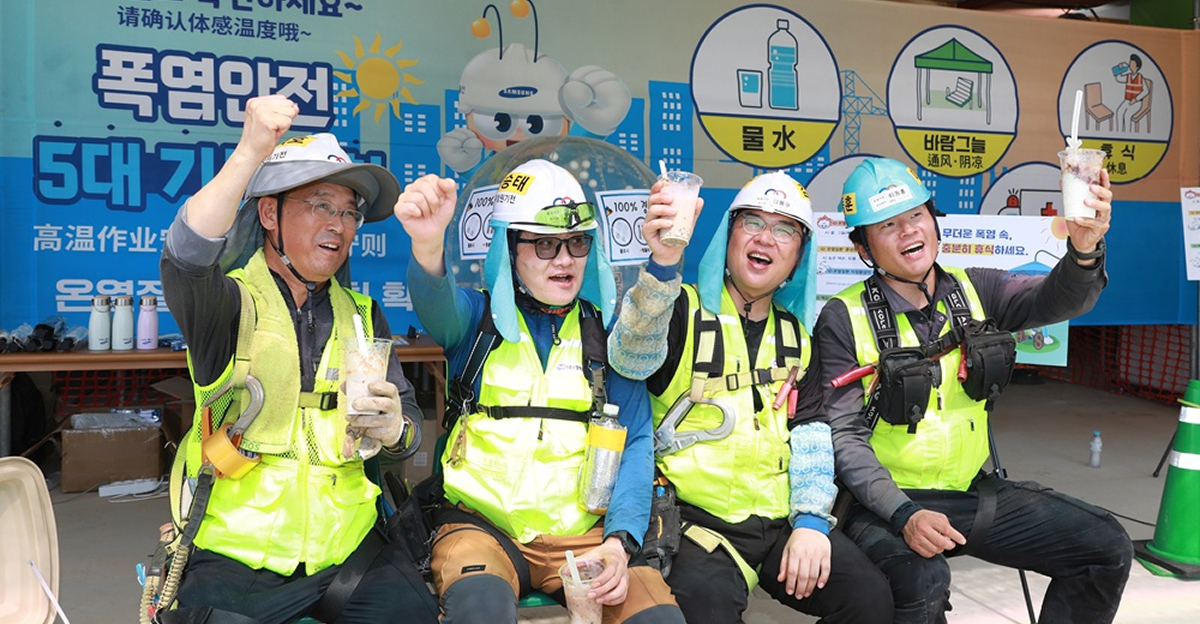
Building in the Heat: How Samsung C&T Is Protecting Construction
August 12, 2025
Samsung C&T Q2 2025 Earnings
[Overall Performance – Revenue: KRW 10.022T, Operating Profit: KRW 753B] [Revenue]Decreased by KRW 983B compared to KRW 11.005T in Q2 2024Increased by KRW 285B compared to KRW 9.737T in Q1 2025 [Operating Profit]Decreased by KRW 147B compared to KRW 900B in Q2 2024Increased by KRW 29B compared to KRW 724B in Q1 2025 < Executive […]
July 30, 2025
Samsung C&T Q1 2025 Earnings
[ Overall Performance – Revenue: KRW 9.737T, Operating Profit: KRW 724B ] [Revenue] Decreased by KRW 1.059T compared to KRW 10.796T in Q1 2024Decreased by KRW 256B compared to KRW 9.993T in Q4 2024 [Operating Profit] Increased by KRW 12B compared to KRW 712B in Q1 2024Increased by KRW 89B compared to KRW 635B in […]
April 30, 2025
Samsung C&T Q4 2024 Earnings
< 2024 Overall Performance > [ Revenue: KRW 42.103T, Operating Profit: KRW 2.984T ] [Revenue] Increased by KRW 207B compared to KRW 41.896T in 2023.[Operating Profit] Increased by KRW 114B compared to KRW 2.870T in 2023. < Q4 Overall Performance > [ Revenue: KRW 9.993T, Operating Profit: KRW 635B ] [Revenue] Decreased by KRW 107B […]
January 22, 2025
ABOUT SAMSUNG C&T
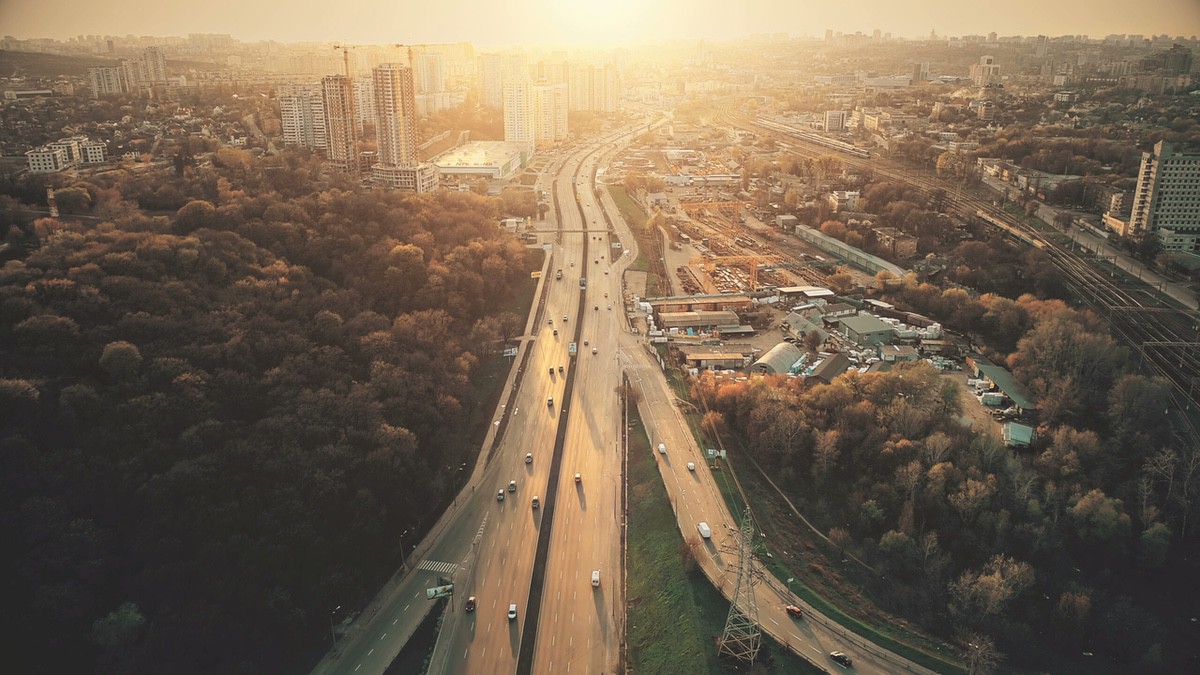
Overview
A quick glance at Samsung C&T
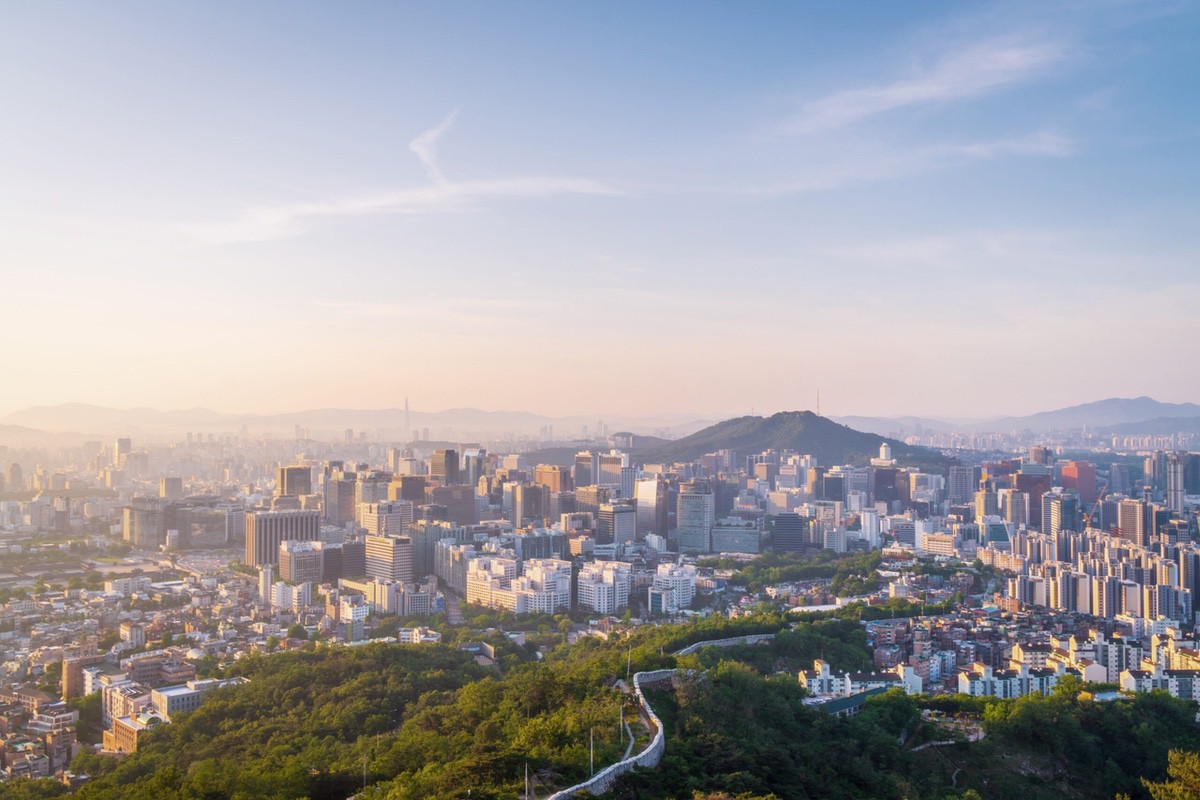
History
How we got to where we are
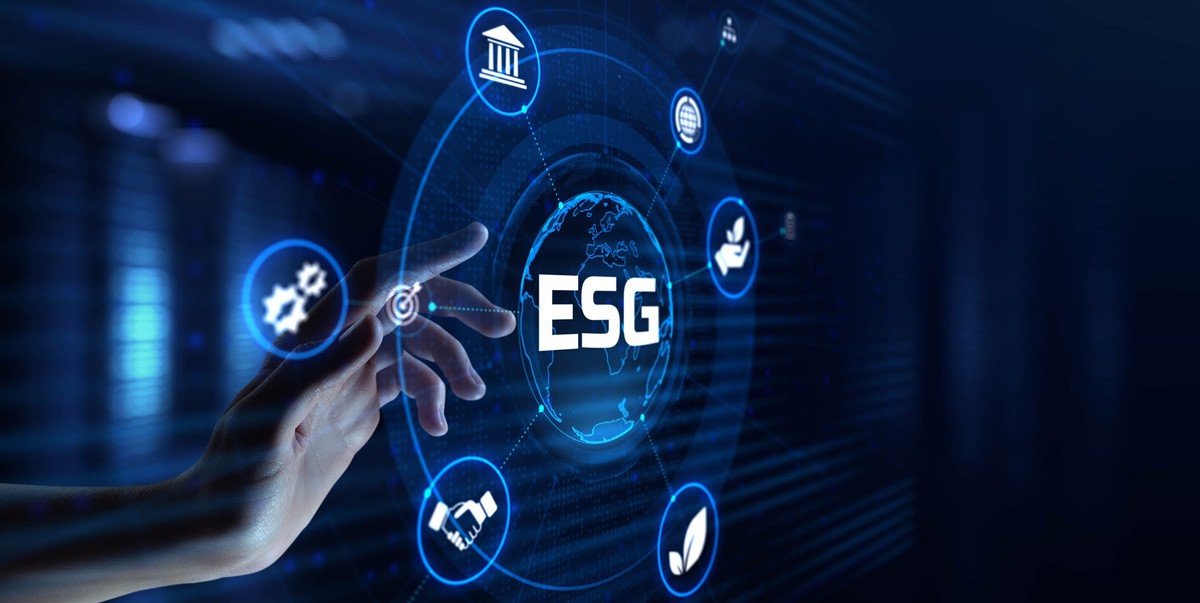
ESG
A strategy and framework
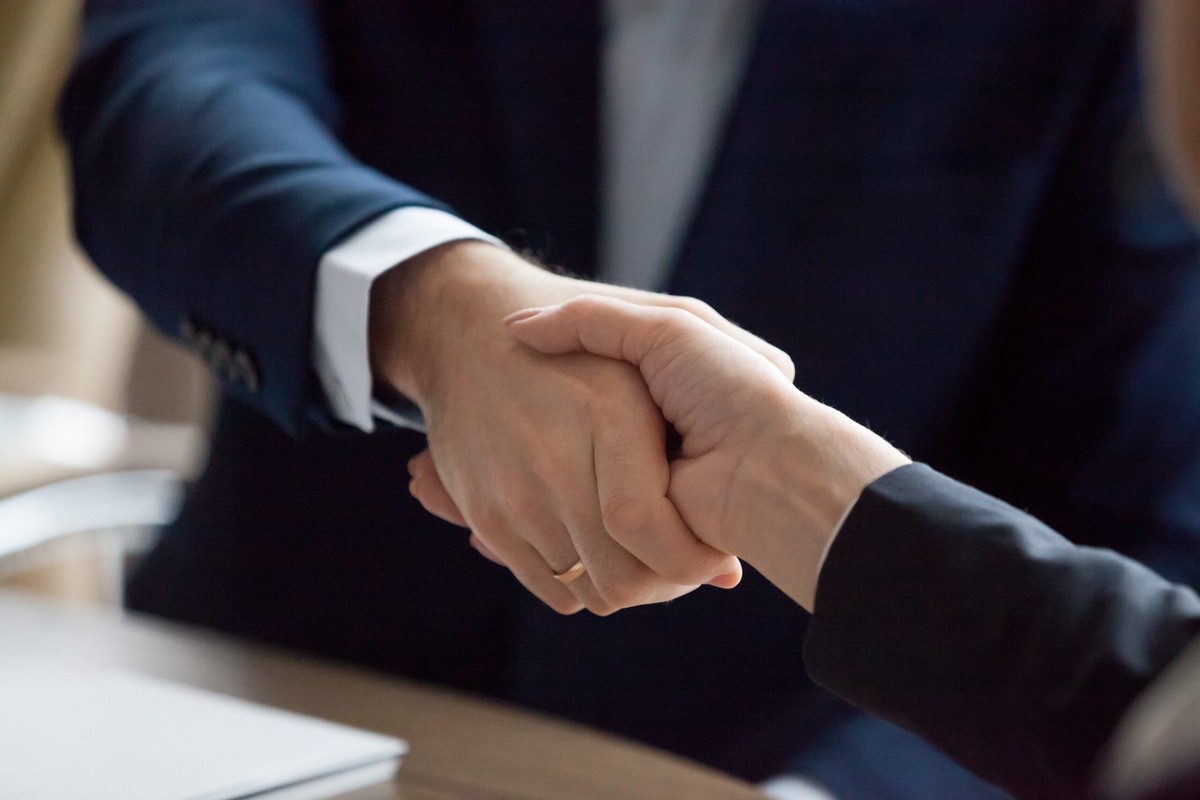
IR
The financial details
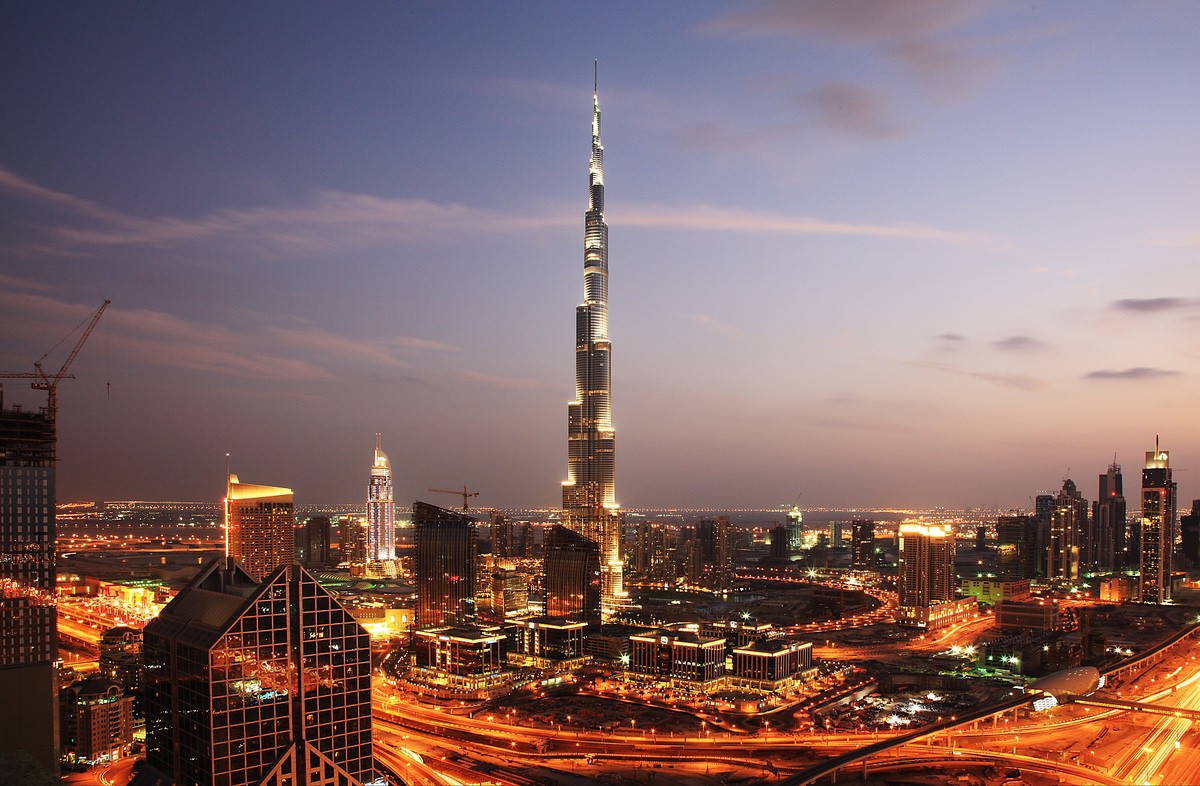
Engineering & Construction
Creating the infrastructure of the future
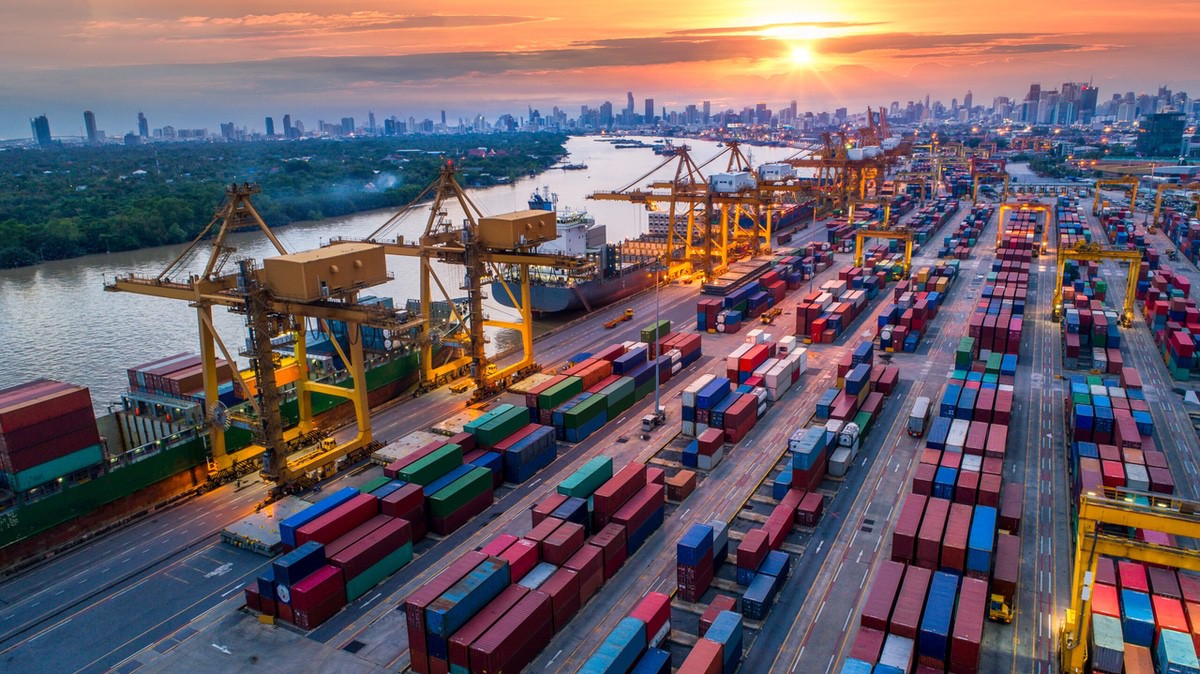
Trading & Investment
Creating global value
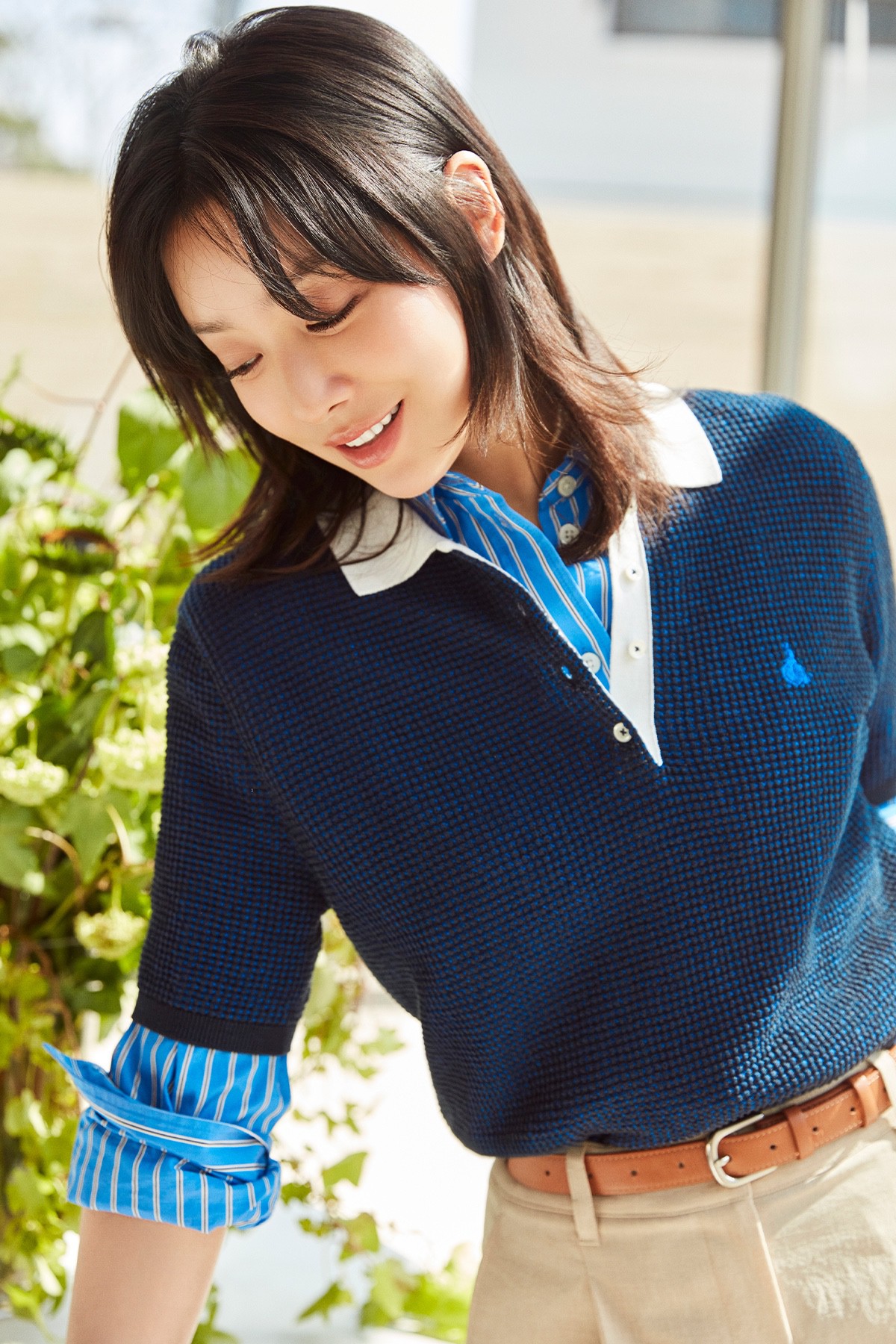
Fashion
Innovation in global lifestyle
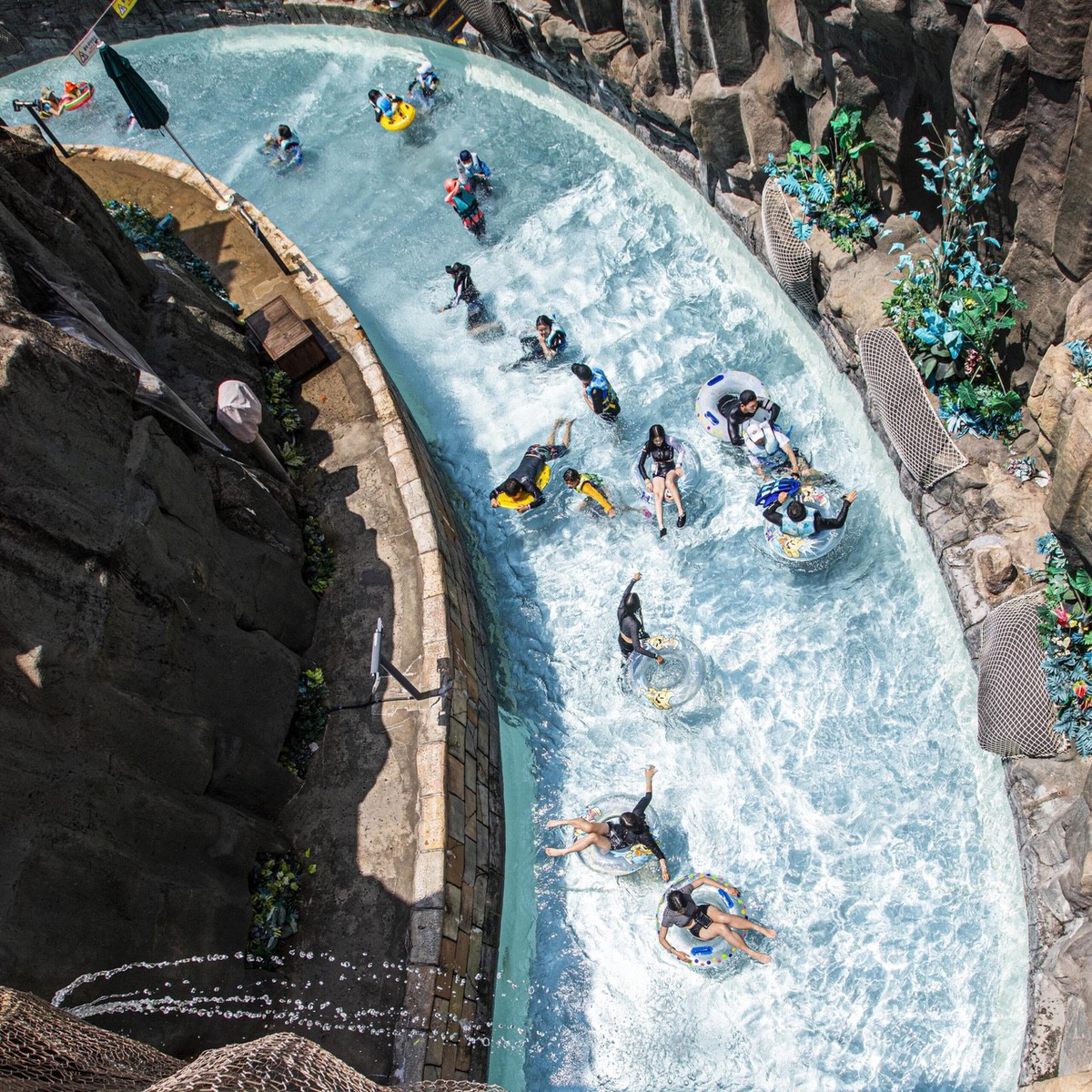
Resort
Designing what can delight everyone
IN NUMBERS
45
Countries
126
Offices
9,380
Employees
61.9 Trillion KRW
Total Asssets
42.1 Trillion KRW
Sales
2.9Trillion KRW
Operating Profit
As of 2024